Do you know which tool to choose for a given dimension? Or do you measure with what is at hand? Maybe you always choose a digital caliper because it’s easiest? A well-selected measuring tool for a given specification will avoid potential quality complaints about the product. If you don’t know what criteria to follow, you’re probably doing it wrong.
Selection of measuring instruments – key rules
First, a few crucial general rules with a simple, but very interesting, example to folow. This will Pinpoint of how a poorly selected tool introduces a huge risk of making a wrong decision regarding compliance with the specification.
What to do when we receive an element to be measured along with a technical drawing? What should you consider when selecting a measuring tool?
- Check the requirements for a given dimension carefully. Specifications should be clearly defined, pay attention to tolerances. Look at the element to be measured, determine whether its measurement is physically possible or whether there are any difficulties. Of course, the situation is different when measuring the shaft diameter of Ø30±0.02 mm, and different when you receive a specification, e.g. measuring the roundness deviation RONt=10µm. In the first case, a hand measuring tool is enough, in the second case, it will be necessary to measure, e.g. using a coordinate measuring machine.
- Define the instrument’s measurement range. Avoid taking a measurement with the instrument when a given measurement occurs at the extreme ends of the range. It is best if the measured dimension is located halfway through the range, of course this is not always possible. Check whether you need additional equipment, e.g. a handle or type of mounting.
- Note: your measurement result is not the actual measurement!
That doesn’t mean you measured wrong…I assume you did everything correctly. The measurement result is so-called observed, it is subject to measurement uncertainty.
Uncertainty of measurement
Measurement uncertainty is a symmetrical interval around the measurement result, which contains the actual value with a certain probability. The sources of uncertainty are different and depend on a given measurement procedure, they may result from: the tool, the measured object, environmental conditions, the person who performs the measurement and the measurement strategy. If you do not investigate the sources of uncertainty, at least check the MPE (Maximum Permissible Error) of the device in the tool documentation. Not to be confused with resolution, i.e. scale. Usually, information about MPE is provided by the manufacturer, sometimes in the user manual MPE is called “accuracy”. In simple words, MPE is the value by which a given instrument can be wrong, it is the symmetrical range in which the measurement result with this tool lies.
Selection of measuring instruments – MPE error
To achieve reliable and appropriate measurement results, the metrological principle is used, which states that the MPE error should be less than 10% of the T tolerance range. However, if this is not possible, the range can be increased, e.g. to 30%T.
E.g. Ø30±0.02 mm, T=0.04 mm, in the case of the MPE<20%T rule, we choose a device with MPE<0.008 mm.
Note 2: The situation becomes more complicated when employees do not have access to technical documentation and instrument manuals. A facilitation often found in enterprises is the selection of a measuring tool to the dimension due to the resolution of the instrument. In short, if T dimension tolerance is in “hundreds”, e.g. ±0.01, we choose a device that will indicate with a resolution
in micrometers. This is a simplification of the MPE<10%T rule. E.g. Ø30±0.02 mm, T=0.04 mm, we choose a digital micrometer with a resolution of 0.001 mm.
Let’s return to listing of our key principles:
- Determine the environmental conditions in which the instrument will operate. Define whether it is necessary, for example, for the device to be waterproof or if it can work at high temperatures.
- If you have already determined the above requirements, check whether you have such a device in your resources. If you need to purchase, look for a suitable supplier.
- Determine who will perform the measurement and check if the person performing the measurement have appropriate knowledge and skills?
- The method of collecting measurement data is also important. Is reading and recording of the measurement from the tool enough? On certain situations data recording needs to be followed by its sharing with other people.
After stating of above conditions there is nothing left to do but measure, quite likely – to measure correctly.
Selection of measuring instruments – example
Please follow through the simple example of how to correctly select a device to measure a seemingly basic element.
Shaft Ø30±0.02 mm. Tolerance field T=0.04 mm.
We have the tools:
Measuring instrument | Range | Resolution | MPE |
Digital caliper | 0-150 mm | 0,01 mm | ± 0,02 mm |
Digital micrometer | 25-50 mm | 0,001 mm | ± 0,003 mm |
Analog caliper | 0-150 mm | 0,02 mm | ± 0,03 mm |
For most of us, our first thought would probably be a digital caliper. Measuring with this instrument is simple. However, look what happens to the measurement result with such a caliper, and what range the result actually falls in. Potentially, all shaft measurement results obtained with these three tools (white points) are within the tolerance zone (marked with a green rectangle). When we take into account the permissible errors of these devices, it turns out that the risk of making a wrong decision is very high.
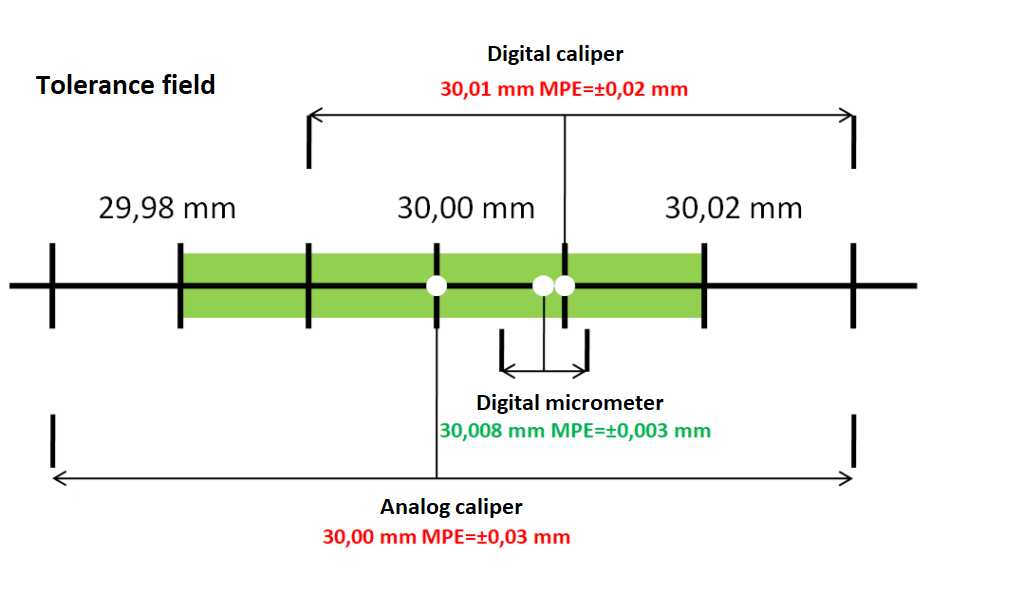
The measurement result obtained with a digital caliper is 30.01 mm, but this is only an observed dimension and may be within the MPE error range, and therefore may fall out of tolerance. If we determine compliance with the specification, we take on a huge risk. The situation is terrible in the case of an analog caliper, even though our measurement results in a nominal value of 30.00 mm. Verify how large the permissible error of such a caliper is – that clearly implies that the error range exceeds the tolerance range. In this case, measurement with the mentioned calipers is unacceptable. Let’s take a closer look at a micrometer. The result is also within the tolerance range, and the permissible error is so small that we do not bear any risk of making an incorrect decision regarding compliance with the specification.
Summary
Measure an element – it seems easy to do, but the trick is to do it well, reliably, responsibly, and most importantly, with an appropriately selected tool.